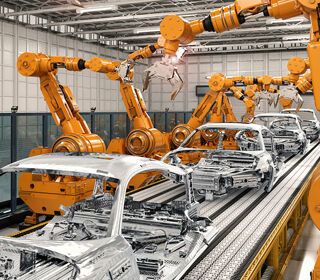
Blog Article
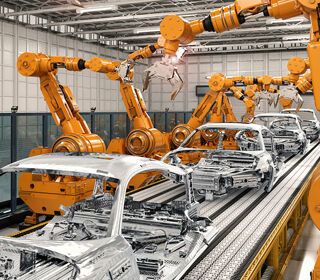
Chances are that you’re familiar with magnesium in some form or another, whether that’s the Mg symbol on the periodic table, as a health supplement, or in manufacturing. Magnesium is an incredibly misunderstood material which has been through a tough time and been tarnished with a bad reputation. Makhan Singh, Business Development Manager for the Institute of Sustainable Futures at Birmingham City University, reveals why the tables turned and what we need to do about it.
As a Business Development Manager for the Institute of Sustainable Futures at Birmingham City University, I develop partnerships and initiate collaborative projects, particularly in manufacturing and automotive sectors, having worked in that space for over 25 years, including roles at Land Rover, Johnson Controls, Britax Seating and Keiper Recaro .
Prior to joining Birmingham City University, I worked with Meridian Lightweight Technologies UK (MLTUK), one of the world’s largest and the UK’s only magnesium High Pressure Die Casting (HPDC) company.
This is why Birmingham City University created a Magnesium Innovation Group and our Annual Magnesium Symposium to bring our exciting research and developments within industry together to change perceptions of this amazing material.
The benefits of magnesium
Magnesium is the lightest structural metal in the world; up to around 70% lighter than steel and between 30-50% lighter than aluminium. It’s the eighth most abundant material in the world, has great heat dissipation properties, 100% recyclable and a fire-retardant material. It has excellent noise, vibration and harshness (NVH) properties too. However, despite all of these amazing properties, Magnesium is a widely misunderstood material.
Why did the automotive and manufacturing industries stop using magnesium?
Magnesium has historically suffered a lot of bad press, which led to many manufacturers discontinuing its use. It’s highly reactive with oxygen, meaning that it’s very hard to extinguish it in the rare occasions that it catches fire. There has been instances throughout history where this has occurred and largely contributed to its misunderstanding.
Why should we start using magnesium again?
Forty years on from its initial ban in the aerospace industry, the International Magnesium Association has proven that magnesium is in fact a fire-retardant material and successfully lifted its ban in the aerospace industry.
Magnesium’s natural properties make it an incredibly advantageous material for the transport sectors. The way it flows and forms during diecasting means it can form very intricate lightweight parts and structures can be made as one piece to simplify design and lower assembly costs. Contrary to popular belief, it actually dissipates heat so it’s much less likely to heat up or catch fire than other metals. This is why mobile phones and laptops often use magnesium parts to prevent damage from overheating. Furthermore, pending contamination conditions, it can often be melted down (past 650°C) and reused, so it’s also very sustainable.
Magnesium has also been largely absent on manufacturing teaching curriculums, particularly at universities. Engineers across the world have a comprehensive knowledge of plastics, carbon fibres, steel and aluminium, but have minimal knowledge about magnesium when designing parts.
How can it be used?
There’s a step change happening after 50 years in the car industry and it is now moving towards the development of electric vehicles to reduce the impact of fossil fuels and climate change. Many vehicle manufacturers are focusing on extending the battery of electric vehicles so they can travel further with each charge, but if we can make these vehicles lighter they will use much less energy. This is just one of the innovative ways magnesium is beginning to be used by the automotive industry.
What have we achieved so far?
In order to kickstart the wide use of magnesium once again, it’s vital that we start to re-educate those with misconceptions to bring it back into the spotlight. Meridian kindly donated £10,000 to Birmingham City University, which allowed us to produce a book together showcasing magnesium and its incredible potential. We’ve received great interest from students and academics at the University, with magnesium-related projects being carried out in engineering, arts, psychology and health faculties. The book was well received by industry and has generated some interesting enquiries which make me feel hopeful that we are succeeding in changing magnesium’s perceptions.
Furthermore, we have already witnessed magnesium being used more widely in the manufacturing and automotive industries in the UK and across Europe. The Jaguar F-Pace, for example, features a lightweight magnesium front end carrier.
What future research is on the cards?
Birmingham City University is working with a number of businesses and national bodies on specific technical projects, PR, art and installation projects. One example is our collaboration with Birmingham Airport to design a magnesium art sculpture in the form of a bird to represent flight. We’re hoping this will get the public engaged and the airlines interested in the magnesium story. We’re also currently working alongside Meridian, compiling a £6m funding application to the government to transform foundries and use digital technology to lift them up into the 21st century so magnesium HPDC parts can be produced with a more modern methodology.
My gut feeling is that demand for magnesium will increase dramatically over the next five years, as will the research, development and specialist knowledge at Birmingham City University in this area.