Evac+Chair International Case Study
Innovative product design transforms neonatal care
Evac+Chair International, based in Birmingham, are a leading manufacturer of evacuation chairs and equipment, ensuring those with restricted mobility are able to be transported quickly and effectively in emergency situations.
What was the client's business challenge?
With high spending on post-neonatal care due to excessive impact during ambulance transportation, Evac+Chair identified the opportunity to solve this challenge by partaking in a Knowledge Transfer Partnership (KTP, part-funded by Innovate UK) to reduce the impact on neonates (babies under four weeks old) during transit in ambulances. In order to achieve this, Evac+Chair enlisted the help of Birmingham City University’s School of Architecture and Design academics to support the design and development of a g-force reduction ambulance trolley that can also safeguard the neonate in the event of an ambulance crash of up to 40MPH.
Evac+Chair InternationalSteve Jinx, Product Development Manager
The use of G-Force data loggers in patient transfers on normal trolleys has been significantly useful, as this knowledge is transferable into many other product development application areas such as the company's paraid medical products division,
How did your service address the client's needs?
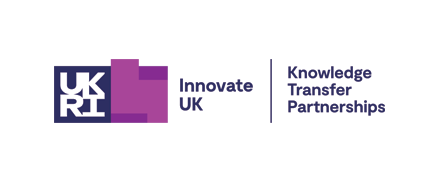
What measurable outcomes did the client experience as a result of your service?
The successful outcome of the KTP has enabled Evac+Chair International to gain international recognition for their safety standards as well as improve sales and develop a more efficient production process. By focusing on reducing g-force and improving products safety standards, Evac+Chair now have new innovative products for sale in home, EU, USA and World markets.
Furthermore, within one month of completing the KTP, the company sold 13 new ambulance trolleys each costing £18,500 (£240,500 in total) to Qatar. Growth in the new Middle Eastern market is expected to continue from this initial order.
Other key benefits include:
-
#1. Greater customer retention
Greater customer retention for renewed orders and new customers worldwide
-
#2. New service contracts
New service contracts for all neonatal ambulance trolleys using IRIS
-
#3. Shorter design to manufacture timescales
Shorter design to manufacture timescales resulting in increased capability of new products
-
#4. Increase in profit margin
Increase in profit margin as a result of continuous new product development techniques developed with Birmingham City University
-
#5. Improved processes
A reduction in the need to design/redesign new parts for existing and new neonatal transporters
-
#6. Enhanced control software
Implementation of a documentation control software has ensured zero errors in version control of its technical drawings for production and assembly.
View more case studies
- METCLOUD - AI and Innovation Journey
- Hadley Group - Innovation in Residential Construction
- Evac+Chair International - Innovative Product Design
- Spectrum - Develops a New Network Monitoring Tool
Enquire about BCU's KTP support
Send an enquiry and a member of the team will be in touch to discuss your needs.