University News Last updated 13 January 2017
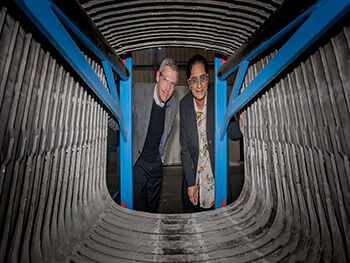
Researchers at Birmingham City University are hoping to transform the fortunes of magnesium this year, by showcasing it as a viable alternative for luxury car makers and the aerospace industry.
It comes as the institution has signed an exclusive partnership with the world’s largest producer of magnesium components, Meridian.
The strategic alliance will see the two organisations work together in the education, research and development of magnesium use, which will place fuel efficiency through weight savings and sustainability at its core.
At 1.8g/cm³, magnesium is the lightest of all structural materials, the eighth most abundant chemical element in the earth’s crust and is 100 per cent recyclable.
Die-cast production
Originating in Strathroy, Canada, Meridian opened its UK facility in July 2003. Today, its Nottinghamshire plant produces around 5,000 net metric tons of die-cast products annually, serving automotive clients such as Jaguar, Land Rover, BMW, Ford, Honda and Volvo.
However, being able to offer bespoke magnesium components for low-volume manufacturers, such as Aston Martin, Bentley and Rolls-Royce, can prove costly using current manufacturing methods, as the costs of tooling and set up become more significant components of a project’s budget.
As part of the new partnership with Meridian, academics from Birmingham City University’s Faculty of Computing, Engineering and The Built Environment and personnel from the company will be investigating new ways to offer more sustainable goods for low-volume manufacturers, whilst making production financially viable for Meridian and its potential clients.
“As being one the world's leading suppliers of innovative, lightweight cast metal solutions for the transportation industry, it is imperative that we remain at the forefront of the machining and casting capabilities of magnesium.
“Our partnership with Birmingham City University will certainly catalyse this, allowing us to benefit from its leading edge research in the field and ensuring that the next generation of engineers continue to experiment with new ways in which to utilise the metal.”
Magnesium Innovation Group
In order for this to come to fruition, the University has established the Magnesium Innovation Group. From this group, 10 academics have been partnered with Meridian employees that best represent their area of expertise, and they will be actively engaging with their partner in the industry for the first half of 2017.
Research findings will be published ahead of a major international magnesium conference, which will be held at Birmingham City University in July this year.
Two psychologists from the University’s Faculty of Business, Law and Social Sciences have also been appointed to the Magnesium Innovation Group. They will spend time interviewing engineers from across the UK and try to understand why there has been a historical aversion to designing products with magnesium, when compared to less sustainable and heavier metals.
Magnesium is produced from sea water, brines and magnesium-bearing minerals which offer unlimited reserves, with an estimated 500,000 metric tons produced each year. It is 75 per cent lighter than steel and 33 per cent lighter than aluminium.
Future uses for magnesium
Current magnesium manufacturing processes create the same amount of waste as product and the Birmingham City University Magnesium Innovation Group will be investigating ways on how value can be created from excess material.
Although magnesium is 100 per cent recyclable, there are currently no plants in the UK that can process the material. However, there is a possibility, for example, that it can be crushed for tablets in the health industry.
Other ideas being discussed at Birmingham City University include reacting magnesium with oxygen and water to create hydrogen, which can be used in the fledgling fuel cell industry, powering cars and smartphones going forward.
“As well as benefiting Meridian’s work here in the Midlands, we hope that our findings can enhance lightweight technologies around the world, ensuring that low-volume manufacturers in the automobile and aerospace industries have access to cost-effective and sustainable magnesium components.”
The partnership was agreed on Friday 13 January at Meridian’s Sutton-in-Ashfield plant with a delegation team from Birmingham City University led by Professor Hanifa Shah, Associate Dean (Research and Enterprise), Faculty of Computing, Engineering and The Built Environment and the senior management team from MLTUK led by Randy Chalmers, Plant Manager.
Institute of Sustainable Futures
The collaboration was made possible thanks to groundwork by the University’s Institute of Sustainable Futures.
Through a range of products, services and facilities supported by more than 300 staff – and underpinned by vigorous research activities – the Institute of Sustainable Futures work within the sustainable futures arena and has gained a reputation as a hub of knowledge, technology and skills-transfer into industry.
“The UK undoubtedly has a renowned science and innovation sector, and this partnership will set out a roadmap that will seek to amplify and identify further opportunities for innovation, future growth and investment. This is very much in tune with the industrial strategy across a number of sectors, such as automotive and aerospace industries.”
The Institute has a track record of working with more than 4,000 companies undertaking close-to-market research and project work focusing on areas such as sensor technology, bioenergy, low carbon, transportation, intelligent buildings and supply chain logistics.